The world’s smallest drum
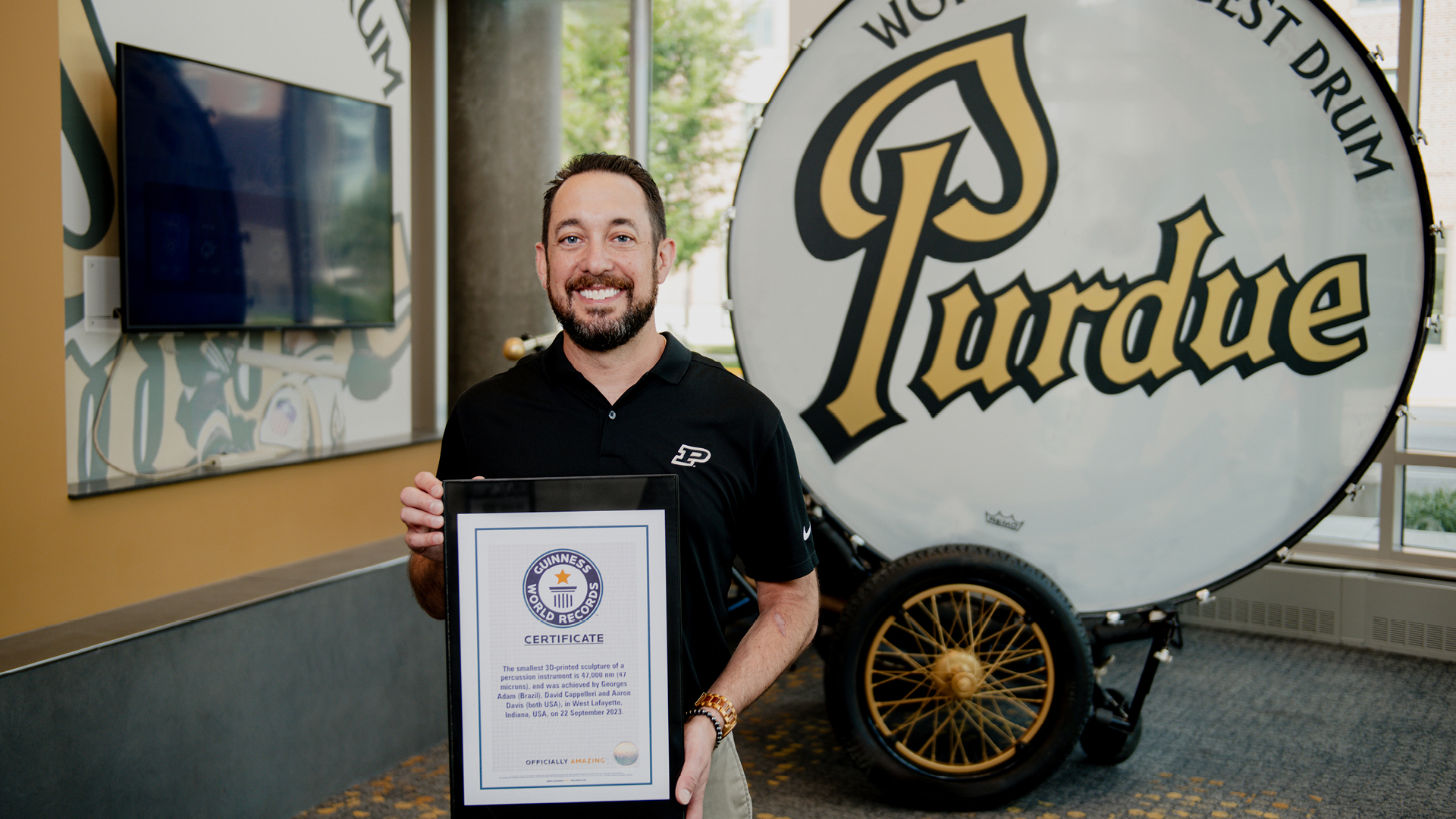
Drumroll, please: Guinness World Records recognized Dave Cappelleri, professor of mechanical engineering and assistant vice president for research innovation, along with his team, for their achievement. (Purdue University photo/Greta Bell)
New 3D printing technology is expanding horizons for microrobotics research on Purdue’s campus
Boilermakers everywhere already know that Purdue is home of the World’s Largest Drum.
But have you heard about the world’s smallest drum? It’s probably not going to get rolled out onto the field at Ross-Ade Stadium for any football games. Even if it were, you wouldn’t be able to see it.
That’s because small means small — about the width of a human hair.
For such a tiny object, it has received attention on a grand scale — it was recently recognized by Guinness World Records as the “smallest 3D-printed sculpture of a percussion instrument.” The team behind its creation received a celebratory certificate.
Dave Cappelleri, professor of mechanical engineering and assistant vice president for research innovation, came up with the idea for the world’s smallest drum to test out the Nanoscribe Photonic Professional GT2 3D printer, which streamlines the production of microscopic materials while pioneering new potential applications in medical treatments. Housed at Birck Nanotechnology Center in Discovery Park District at Purdue, the printer is the first of its kind in operation in Indiana and was acquired with a financial award from the US National Science Foundation.
Alongside Georges Adam (PhD mechanical engineering ’22), a postdoctoral researcher in microrobotics, they also printed microscopic replicas of other Purdue landmarks: the Class of 1939 Water Sculpture (commonly known as the Engineering Fountain), the Unfinished Block P sculpture — and Purdue’s official mascot, the Boilermaker Special.
“Everyone knows what the World’s Largest Drum looks like. People know what the Boilermaker Special looks like. So now we can tell them, this is the same thing — but less than a human hair in diameter. It’s a good visual,” Cappelleri says.
With their Purdue-themed test run complete, the printer is revolutionizing how Purdue microrobotics researchers engage with the field and vastly expanding the potential benefits of mobile microbots. Asked to define the term, Cappelleri explains that a mobile microrobot is an untethered device, less than a millimeter in size, that can be controlled wirelessly.
“We can streamline the manufacturing to make things even smaller, with more detail — and faster,” Adam explains. “So instead of taking about a week to make robots, now I can do them in a few hours.”
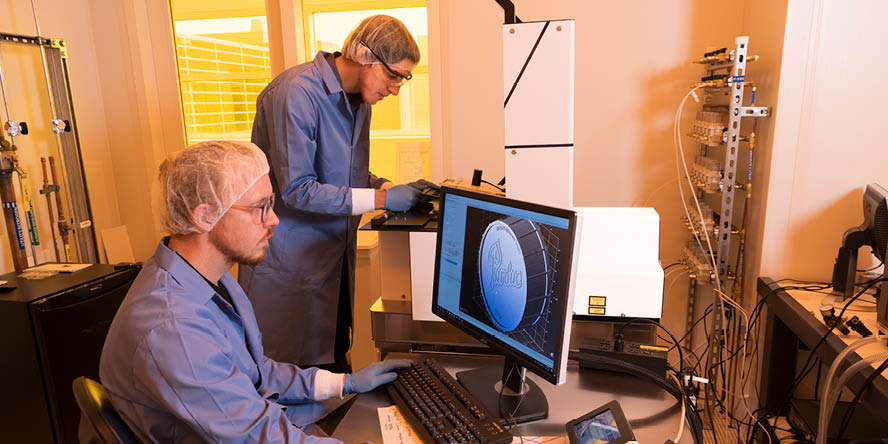

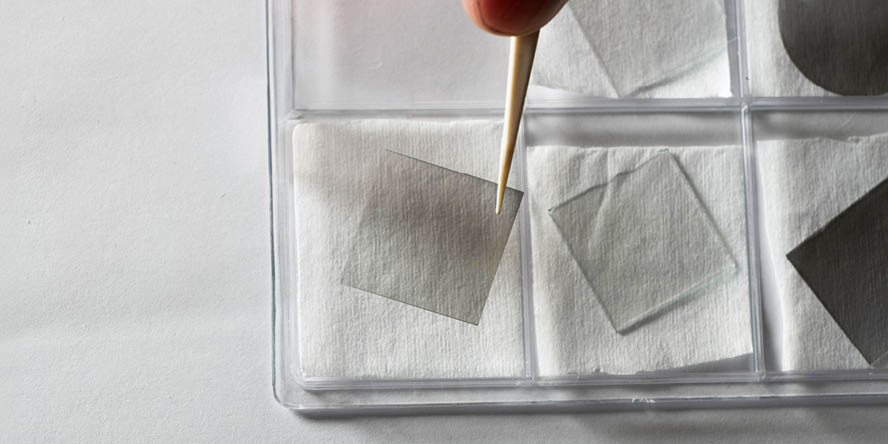
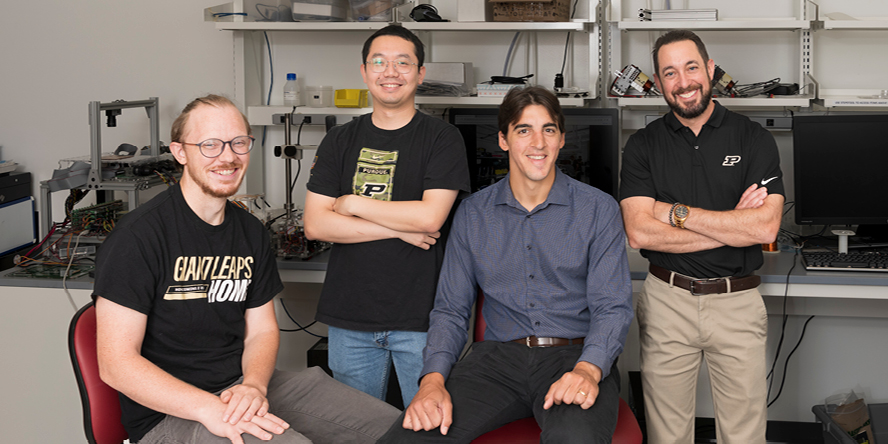
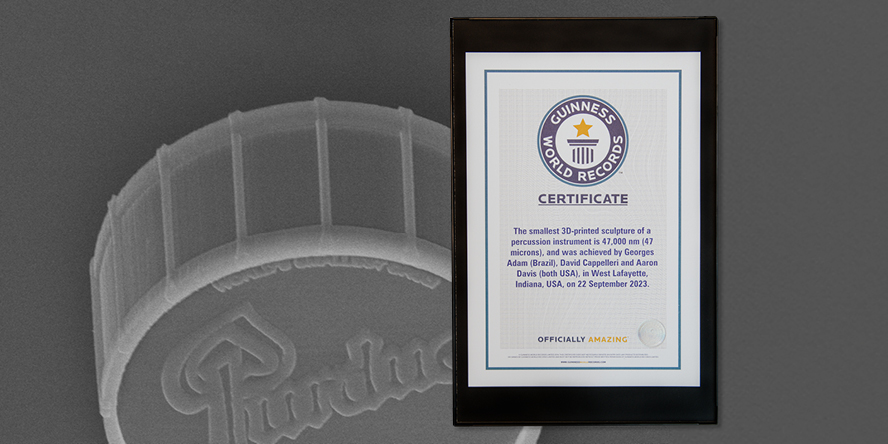
Tiny technology, far-reaching frontiers
Microrobotics has far-reaching potential, including in biomedical applications.
“Microrobots can go places that you just can’t get to with larger-scale robots,” Cappelleri says. “By developing these robots to go into the body, it allows you to do some really precise operations, whether that be deliver a drug, manipulate a cell, characterize an object, etc.”
Working on a micro scale comes with its share of new opportunities — and challenges, including the need for an external stimulus to power the microrobots’ movement.
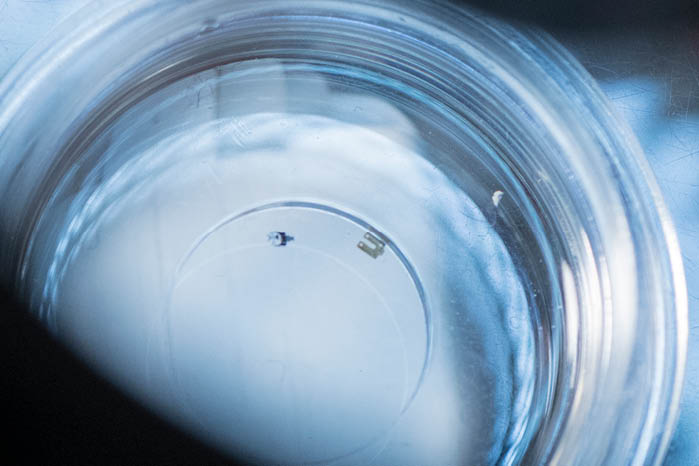
A microrobot in testing facilities on Purdue’s campus, where technological advances are allowing researchers to exert greater control over microrobots. (Purdue University photo/John Underwood)
“Since the robots are very small, we can’t put batteries on them, and we need some kind of external field to control the robot,” Cappelleri explains. “So we use magnetics and magnetic fields. As long as the robots have some magnetic properties, we can use that to drive them around. We have vision-based control, which gives us an image of the robot so we know where it is, and we can tell it where to go using a joystick, or it can be done autonomously by preprogramming a desired location. Based on this information and the real-time microrobot position, the system will calculate the appropriate magnetic field settings to drive the robot to that goal location.”
Microrobotic technology has come a long way in a relatively short time.
“When I was in grad school, I did work in microrobotics with similar micromanipulation systems to what Georges has worked on,” Cappelleri says. “At the time, the field of mobile microrobotics was just starting. When we got started, we were just trying to see if we could fabricate some kind of microscopic objects with magnetic properties and get them to move using a magnetic coil system. And that took a while.”
Back in 2010, Cappelleri competed in the first-ever 2-Millimeter Dash. The challenge: move a microscale robot two millimeters in a straight line faster than your competitors.
In addition to testing the microrobots’ speed and mobility, the competition featured a performance challenge in which teams had to use their microrobot to insert pegs in predesignated places as well as a freestyle event testing microrobots for autonomy, power management, system reliability and task complexity.
If you think about the mobile robotics level, like your Starship robots, they’re following waypoints to get to some location on campus. If you have an accurate map of where the robot is going to be in the body, you can do the same thing.
Dave Cappelleri
Professor of mechanical engineering
In the years since, the complexity of tasks and environments that microrobots can navigate has increased.
“Once we could get them to move in a straight line, we said, ‘OK, now can we get them to go in different directions? Can we go in liquid environments? Can we do useful tasks with them?’” Cappelleri says.
Robots are no strangers to West Lafayette.
In 2019 Purdue became one of the first colleges in the United States to welcome Starship delivery robots. Ever since, a fleet of more than 30 robots has become a campus fixture.
While operating on a different scale, the technology that allows a Starship robot to deliver your Starbucks or Jimmy John’s isn’t so different from the technology that powers microrobots to move through the human body.
“If you think about the mobile robotics level, like your Starship robots, they’re following waypoints to get to some location on campus,” Cappelleri says. “If you have an accurate map of where the robot is going to be in the body, you can do the same thing.”
The Nanoscribe 3D printer is opening up even more doors for microrobotic technology.
“Now we can make these 3D structures at the micro and even the nanoscale,” Cappelleri says. “That opens up a lot of design space where before we were kind of constrained in what we could do.”
“It’s a totally different application procedure,” Adam adds. “Before, we would go into a cleanroom and have to go through this whole time-consuming process. This new technology, it’s basically a laser printer that you put a little drop of a liquid of a photopolymer that will react with a laser light. The laser can focus on a really, really small area and basically turn it into a plastic that will become solid. Once that’s done, we wash away the rest of the liquid, and you are left with the shape you want.”
“Going from 2D to 3D is big,” Cappelleri says. “It opens up a whole new realm of possibilities. We’re also now printing helical robots that kind of look like a corkscrew or fusilli pasta with a magnetic head, and we can use them to rotate and swim. That’s something that you really can’t do with standard lithography or cleanroom fabrication techniques, so it opens up new modes of locomotion for these designs.”
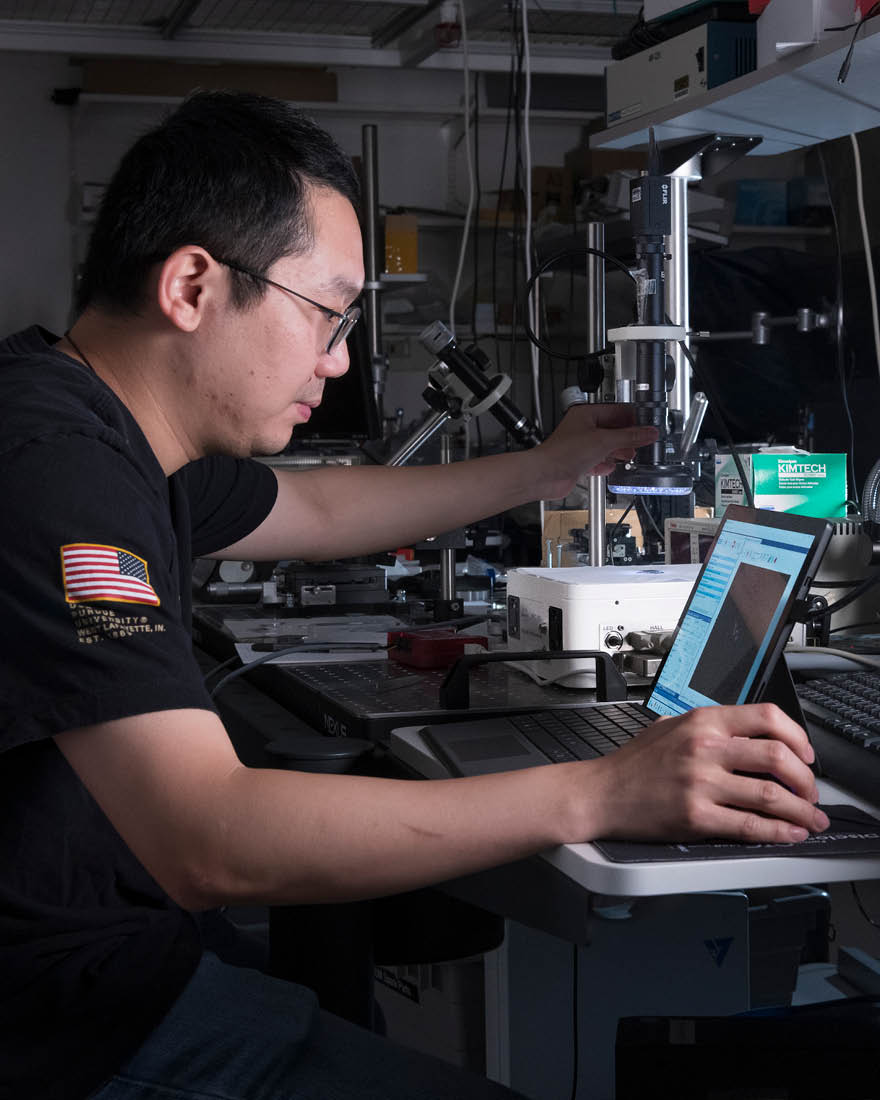
Campuswide collaboration
These technological advances have opened the door to new opportunities for cross-campus collaboration.
“In general, robotics is interdisciplinary — and if you work in microrobotics, even more so,” Cappelleri explains. “Not only do you need people that can design and make them, you need a materials person, you need chemistry expertise, you need imaging expertise and controls. So you need a big interdisciplinary team.”
Adam and Cappelleri work closely with two faculty members in biomedical engineering: Luis Solorio and Craig Goergen.
“Dave had developed these really interesting robots, and he was hoping to transition them into more biological applications,” says Solorio, associate professor of biomedical engineering. “We brainstormed around several different projects, but the one that we ended up getting NIH funding for was to treat ulcerative colitis. With this new technology, we can develop a precision strategy to steer these small robots to the area of interest and then develop a controlled release payload system so that we can locally deliver therapeutics.”
Solorio and Goergen’s expertise positions them as critical partners in developing the full possibilities of microrobotics technology.
“Craig is an expert in ultrasound imaging and in vivo animal studies, and then Luis is a drug payload and control release expert,” Cappelleri says.
“Luis and I have offices down the hall from each other,” says Goergen, the Leslie A. Geddes Professor of Biomedical Engineering. “We’ve always been talking about different ways we could work together, but this was a new technology that we could both really help with optimization and development.”
For Goergen, one of the exciting aspects of this new technology is its far-reaching possibilities for development in treating different diseases.
“I love that Dave isn’t set on one disease or one patient,” he says. “We’re thinking about colon cancer, irritable bowel syndrome, ovarian cancer, uterine fibroids and all these different possible ways that people could benefit from this technology.”
“With these microrobots that Dave developed, you have a lot more control,” Solorio says. “It’s less of a passive passenger with some active components. You’re physically able to put it where you want it to go.”
Ultimately, this means the potential to access more hard-to-reach places in the body with less invasive procedures.
“The most exciting thing for me is having really good students like Georges and turning them loose and seeing what they can come up with,” Cappelleri says. “If you can think of it, you can make it. I’m excited to see what kind of things we can come up with now that we have this new tool in our toolbox.”
All of the possibilities make it possible for researchers and students to only be limited by their own imagination and march to the beat of their own drum.
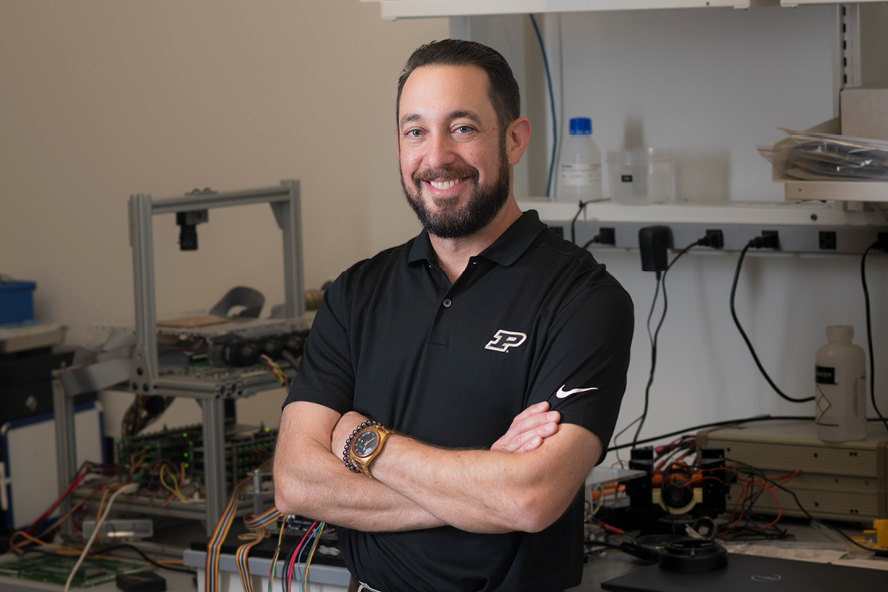
The most exciting thing for me is having really good students like Georges and turning them loose and seeing what they can come up with.
Dave CapPelleri Professor of mechanical engineering